Thread for Screw Tutorial/de: Difference between revisions
No edit summary |
No edit summary |
||
Line 87: | Line 87: | ||
[[File:thread-by-horz-profile-profileMake.png|1000px]] |
[[File:thread-by-horz-profile-profileMake.png|1000px]] |
||
⚫ | |||
<div class="mw-translate-fuzzy"> |
|||
# erstelle eine Helix1 mit einer Höhe, die der Steigung entspricht, und einer Steigung, die der Gewindesteigung entspricht, und einem Helixradius von 0,42*Nenndurchmesser des Gewindes. |
|||
⚫ | |||
# trage das Schnittprofil entlang der Helix1 aus. Hake an ''Erzeuge Volumenkörper'' und ''Frenet''. |
|||
# Erstellen Sie eine Helixkurve, bei der die Höhe und die Steigung gleich der Gewindesteigung sind und der Radius gleich 0.42 mal Gewindedurchmesser ist. |
|||
# Erstelle einen Kreis mit dem Nennradius des Gewindes in der x-y-Ebene. |
|||
# '''Wichtig''': Das zuvor erstellte Profil muss nun in Z-Richtung vollständig unterhalb der Helix liegen! Dies kann entweder durch eine Verschiebung der Helix nach oben oder eine Verschiebung des Profils nach unten realisiert werden. |
|||
# Erstelle eine Fläche aus dem Kreis. (Part Arbeitsbereich: erweitertes Dienstprogramm zum Erstellen von Formen oder [[Draft Upgrade/de|Entwurf Hochstufen]] und ErstelleFläche = true) |
|||
# Extrudieren Sie das Profil entlang der Helixkurve mit dem Sweep-Werkzeug [[Image:Part_Sweep.png|16px]] (''Erzeuge Volumenkörper'' und ''Frenet'' müssen aktiv sein). |
|||
# die Fläche mit dem Sweep Profil schneiden# einen Klon aus dem Schnitt erstellen (Entwurf Arbeitsbereich) |
|||
# Zeichnen Sie einen ausgefüllten Kreis in die XY-Ebene, dessen Radius dem Radius des Gewindes entspricht. |
|||
# Herabstufung des Klons, um einen Draht zu erlangen. (Entwurf Arbeitsbereich) Dieser Draht ist das horizontale Profil, das für diese Methode benötigt wird. |
|||
# Wählen Sie erst den Kreis und dann den zuvor entstandenen Volumenkörper aus und klicken Sie auf ''Ausschneiden'' [[Image:Part_Cut.png|16px]]. |
|||
# Erstelle eine Spirale mit dem Radius des Nennradius des Gewindes und einer Steigung des Gewindes und der Höhe des benötigten Gewindes. |
|||
# Erstellen Sie eine Kopie des resultierenden Objektes (Arbeitsbereich Part > Einfache Kopie erstellen ). |
|||
# Trage den Draht entlang der Spirale aus. Hake Vollmaterial und Frenet an. |
|||
# Wandeln Sie die Schnittfläche in einen Draht um (Arbeitsbereich Draft > Herabstufen [[Image:Draft Downgrade.png|16px]]). |
|||
⚫ | |||
# Erstellen Sie eine Helixkurve, deren Steigung gleich der Gewindesteigung und deren Durchmesser gleich dem Gewindedurchmesser ist. Die Höhe der Kurve ist beliebig wählbar. |
|||
# Nutzen Sie das Sweep-Werkzeug, um den beim Herabstufen erhaltenen Draht entlang der gerade erstellten Helixkurve zu extrudieren (''Erzeuge Volumenkörper'' und ''Frenet'' müssen aktiv sein). |
|||
⚫ | |||
</div> |
|||
Diese Vorgehensweise basiert auf einem [http://forum.freecadweb.org/viewtopic.php?f=3&t=6506#p52558 Forumseintrag von Ulrich1a] mit geringfügigen Anpassungen. |
Diese Vorgehensweise basiert auf einem [http://forum.freecadweb.org/viewtopic.php?f=3&t=6506#p52558 Forumseintrag von Ulrich1a] mit geringfügigen Anpassungen. |
Revision as of 22:17, 23 January 2020
Thema |
---|
Modellierung |
Niveau |
Fortgeschrittene |
Zeit zum Abschluss |
Autoren |
DeepSOIC, Murdic |
FreeCAD-Version |
0.14 oder neuer (je nach Methode) |
Beispieldateien |
Siehe auch |
None |
Einleitung
Dieses Tutorium ist eine Sammlung von Techniken zur Modellierung von Schraubgewinden in FreeCAD.
Von der Modellierung von Gewinden wird abgeraten, da sie sowohl den Modellierungskern als auch die Renderingseite stark belastet. Die Gewindeformen benötigen viel Speicherplatz, und mit nur einem Gewinde in einem FreeCAD Projekt kann die Dateigröße leicht in den Megabyte Bereich steigen. Es gibt jedoch einige Situationen, in denen es wichtig ist, den Thread bis ins Detail zu modellieren, und dafür ist das Tutorial gedacht.
Methode 0. Eins aus der Teilebibliothek beziehen
Die Verwendung von Modellen, die andere Leute geschaffen haben, ist einfach und zeitsparend. Sieh dir Makro SCHRAUBEN an, eine Benutzeroberfläche zum Einfügen von Standardteilen aus der SCHRAUBEN Bibliothek.
Methode 1: Verwendung von Macros
Mit dem beliebten Macro Screw Maker, erstellt von ulrich1a, oder dem zusätzlichen Arbeitsbereich Fasteners Workbench, erstellt von shaise (link to GitHub), können oftmals passende dreieckige Standardgewinde generiert werden.
Methode 2: Schummeln mit gestapelten Scheiben
Dies ist ein guter Weg, um Gewinde grob zu visualisieren und dabei die Geometrie möglichst einfach zu halten. Da jedoch kein tatsächliches Gewinde erzeugt wird, ist diese Methode für herzustellende Bauteile normalerweise ungeeignet.
Die Idee hierbei ist, ein nicht-schraubenförmiges Gewinde zu erzeugen und scheibenförmig zu stapeln. Solch ein Pseudogewinde ist auf den ersten Blick nur schwer von einem tatsächlichen Gewinde zu unterscheiden und lässt sich deshalb in bestimmten Situationen (z.B. FEM-Simulationen) verwenden.
Methode 3: Ein vertikales Profil entlang einer Kurve extrudieren
Die Idee ist sehr einfach: Erstellen eines Profils und anschließendes Extrudieren (Sweep ) des Profils entlang einer helixförmigen Kurve (Helix
). Dabei müssen die Checkboxen Erzeuge Volumenkörper und Frenet aktiviert sein, damit später noch Bool'sche Operationen wie z.B. Vereinigen
oder Ausschneiden
auf das Ergebnis anwendbar sind und zudem keine Verdrillungen entstehen.
Das Resultat ist eine Spule mit dem gewünschten Profil. Um daraus ein Gewinde zu machen, muss das Ergebnis der Operation mit einem Zylinder oder einer Bohrung vereinigt
werden. Mit weiteren Bool'schen Operationen können zudem die abrupten Enden der Spule beseitigt werden.
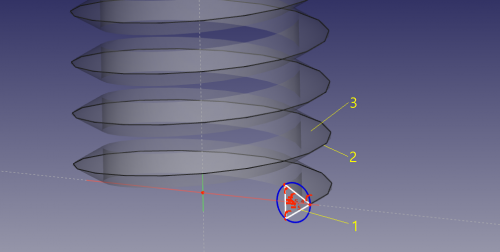
Tipps und Tricks
Regel 1: Die Kurve darf sich nicht selbst schneiden oder berühren, da sonst ein ungültiger Festkörper entsteht. Versuche, das Ergebnis zu vereinigen oder auszuschneiden, werden sehr wahrscheinlich scheitern. Nichtsdestotrotz kann dieses Problem im 3D-Druck oder für Visualisierungen vernachlässigbar sein.
Regel 2: Behalten Sie im Hinterkopf, dass das Werkzeug Helix in FreeCAD nicht immer präzise genug arbeitet. Als Folge kann es passieren, dass beim Vereinigen der Gewindespule mit einem Zylinder Probleme auftreten. Im Allgemeinen sollten geometrische Verknüpfungen zwischen Elementen, die mit dem Werkzeug Sweep
erzeugt wurden und anderen Elementen besser vermieden werden.
Tipp 1: Der Radius der Helix ist unbedeutend, falls kein kegelförmiges Gewinde entstehen soll. Bedeutend sind nur die Steigung und die Höhe der Kurve, d.h. es die Kurve kann für verschiene Gewinde mit gleicher Steigung wiederverwendet werden.
Tipp 2: Halten Sie das Gewinde möglichst kurz, denn bei längeren Kurven kann es Probleme mit den Bool'schen Operationen geben. Stattdessen kann ein kurzes Stück des Gewindes mit dem Werkzeug Draft Array stapelweise wiederverwendet werden.
Vor- und Nachteile
+ Sehr realitätsnahes Verfahren zum Definieren von Gewindeprofilen
+ einfach zu verstehen
+ keine Probleme beim Generieren von Polygongittern des 3D-Modells (im Gegensatz zu Methode 4)
- da sich die Verlaufskurve nicht schneiden darf, ist es fast unmöglich ein lückenloses Gewinde ohne zylindrische Flächen zu erzeugen
- Bool'sche Operationen werden für brauchbare Ergebnisse benötigt, was den Zeitaufwand und die Fehleranfälligkeit erhöht
- Gewinde mit vielen Windungen sind problematisch
Methode 4: Ein horizontales Profil entlang einer Kurve extrudieren
Die Idee hinter dieser Methode ist es, einen horizontalen Querschnitt des Gewindes entlang einer Helix-Kurve zu extrudieren. Das Hauptproblem dabei ist es, das richtige Profil für ein bestimmtes Gewinde zu finden.
Wenn jemand einen Kreis als horizontales Profil verwendet, wobei der Kreis nicht im Ursprung liegen darf, da er die Tiefe des Gewindes definiert, so wird das Gewindeprofil sinusförmig.
Um das übliche Sägezahnprofil zu erhalten, muss ein Paar von archimedischen Spiralen als Draht vereinigt werden. Das Ergebnis hat eine Herzform, die kaum von einem Kreis zu unterscheiden ist, falls die Gewindetiefe klein gegenüber dem Gewindedurchmesser ist (das oben sichtbare Bild zeigt den gegenteiligen Fall).
Generieren des Profils
Es ist nicht einfach das horizontale Profil so zu bestimmen, dass ein bestimmtes vertikales Profil entstehen wird. In einfachen Fällen, z.B. dreieckige oder trapezförmige Profile, kann es von Hand konstruiert werden. Alternativ kann es auch konstruiert werden, indem das Gewinde zunächst mit Methode 3 erstellt wird und dann der Schnitt mit einer horizontalen Fläche erzeugt wird (Schnitt ).
Profil für ein dreieckiges Gewinde
- Erstellen Sie eine (archimedische) Spirale in der XY-Ebene
- Setzen Sie die Anzahl der Windungen auf 0.5
- Der Radius der Spirale sollte dem Innenradius des Gewindes entsprechen
- Das Wachstum muss gleich dem Doppelten der Schnitttiefe des Gewindes sein.
- Spiegeln Sie die Spirale gegen die XY-Ebene (Spiegeln
)
- Vereinigen Sie beide Spiralen, um einen geschlossenen Draht zu erhalten (Vereinigung
)
Fertig!
Profil bei beliebigen Querschnitten
- ein (vertikales) Schnittprofil erstellen. Stelle sicher, dass die Höhe der Skizze mit der Steigung des benötigten Gewindes übereinstimmt.
- erstelle eine Helix1 mit einer Höhe, die der Steigung entspricht, und einer Steigung, die der Gewindesteigung entspricht, und einem Helixradius von 0,42*Nenndurchmesser des Gewindes.
- trage das Schnittprofil entlang der Helix1 aus. Hake an Erzeuge Volumenkörper und Frenet.
- Erstelle einen Kreis mit dem Nennradius des Gewindes in der x-y-Ebene.
- Erstelle eine Fläche aus dem Kreis. (Part Arbeitsbereich: erweitertes Dienstprogramm zum Erstellen von Formen oder Entwurf Hochstufen und ErstelleFläche = true)
- die Fläche mit dem Sweep Profil schneiden# einen Klon aus dem Schnitt erstellen (Entwurf Arbeitsbereich)
- Herabstufung des Klons, um einen Draht zu erlangen. (Entwurf Arbeitsbereich) Dieser Draht ist das horizontale Profil, das für diese Methode benötigt wird.
- Erstelle eine Spirale mit dem Radius des Nennradius des Gewindes und einer Steigung des Gewindes und der Höhe des benötigten Gewindes.
- Trage den Draht entlang der Spirale aus. Hake Vollmaterial und Frenet an.
Fertig.
Diese Vorgehensweise basiert auf einem Forumseintrag von Ulrich1a mit geringfügigen Anpassungen.
Die einzelnen Schritte werden außerdem in folgendem Video von Gaurav Prabhudesai gezeigt und erläutert: http://www.youtube.com/watch?v=fxKxSOGbDYs
Vor- und Nachteile
+ Das resultierende Gewinde ist direkt verwendbar
+ Weniger oder sogar keine Bool'schen Operationen notwendig, sodass die Rechenzeit deutlich geringer ausfällt als bei Methode 3
+ Endflächen der Gewinde sind schön gerade geschnitten
+ Längere Gewinde sind problemlos möglich, falls keine Bool'schen Operationen notwendig sind. Andernfalls ist es kaum besser als Methode 3.
+ Lückenlose Gewinde sind kein Problem
- Definieren des Profils ist aufwendig und kompliziert
- Beim Umwandeln des 3D-Modells in ein Polygongitter kann es, je nach verwendetem Algorithmus, zu Problemen kommen. Dabei zeigt Mefisto die besten Ergebnisse.
- hoher Speicherverbrauch [1]
Methode 5: Lofting between helical extruded faces
Idee
Helical splines will extrude coaxial faces that are able to be lofted, while FreeCAD's parametric helix won't. It takes two helical splines to define a thread. Those two can be scaled from a library spline, then located and extruded appropriately to get the form right.
FreeCAD's parametric helixes aren't truly helical, but helical b-splines aren't difficult to lay out. One manual method is to array dodecagons (12-sided polygons) with 5mm radius/10mm diameter at 1/12mm (0.08333.mm) z intervals and trace splines from vertex to vertex in ascending and rotating order, and to consider doing it once with, say, 10 turns, so that that spline can be re-used as a library file for import and reuse. It's convenient to use 10mm diameter/1mm pitch for ease of scaling. If you are doing it manually, drawing a Dwire and then converting it to a b-spline is easier than drawing a spline. Dwires don't have curvature computed while being drawn, so they follow the cursor and snap more obediently.
Once the splines are scaled to the right size and located so that the loft will have the right included angle between the thread flanks, they're extruded along their axis, a pitch length's worth for the inner spline, the outer pitch/8.
ISO and other threads have relieved, ie flat, inner and outer edges rather than sharp, which suits FreeCAD users with this method, because we can loft to the helical face at the nominal fastener size, while an inner face can't be lofted to an outer edge spline because a face is a closed profile, a spline is open. ISO standard says the nominal size of external threads have a face width pitch/8. The picture shows how the geometry is arranged, and the helical faces that result. Then, loft between the faces, and then a cylinder that gives the inner helical face, which ISO puts at pitch/4 width, is added to the threads.
This method produces reliable solids that boolean properly. While it doesn't produce "parametric" screw threads in standard sizes in the sense of having simple access to form by fastener size, it's an easy way of producing an accurate library for reuse, and models of specialised forms like ACME, or Archimedian screws, are also uncomplicated as one-offs.